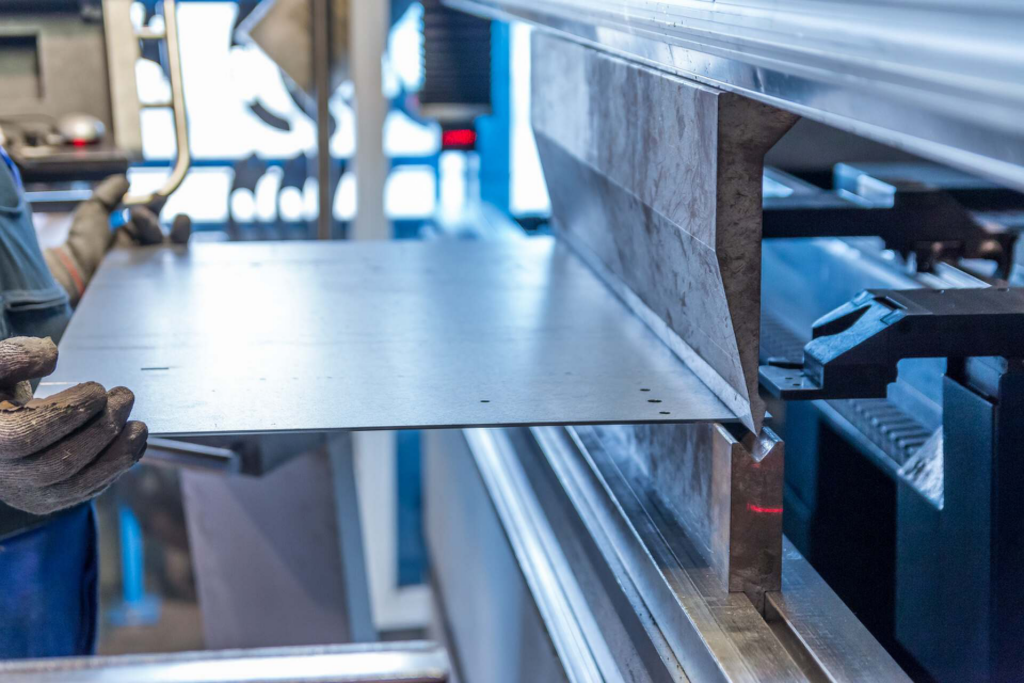
Source: pixabay
Finition en acier inoxydable, qui était souvent utilisé comme apparition du matériau, est un composant important pour de nombreux produits. Donc, Le choix d'une finition en acier inoxydable approprié semble être crucial. C'est l'apparence visuelle du métal et est créée à travers diverses méthodes de traitement, y compris roulement, polissage, et explosion. Vous cherchez probablement une longue durée de vie, Résistance à la corrosion et besoins à faible maintenance. La bonne finition est le moyen de garantir que l'acier inoxydable se comportera comme prévu.
L'option généralement basée sur les différences intrinsèques entre diverses industries. Par exemple, La surface rugueuse correspond au processus avant de peindre et de coller. Néanmoins, Lors de la procédure de mélange, Une surface lisse sera meilleure. Pour certains produits, la valeur de l'apparence comme les architectures et les applications de cuisine, L'esthétique des apparences doit être pensée en premier.
Finitions en acier inoxydable communes
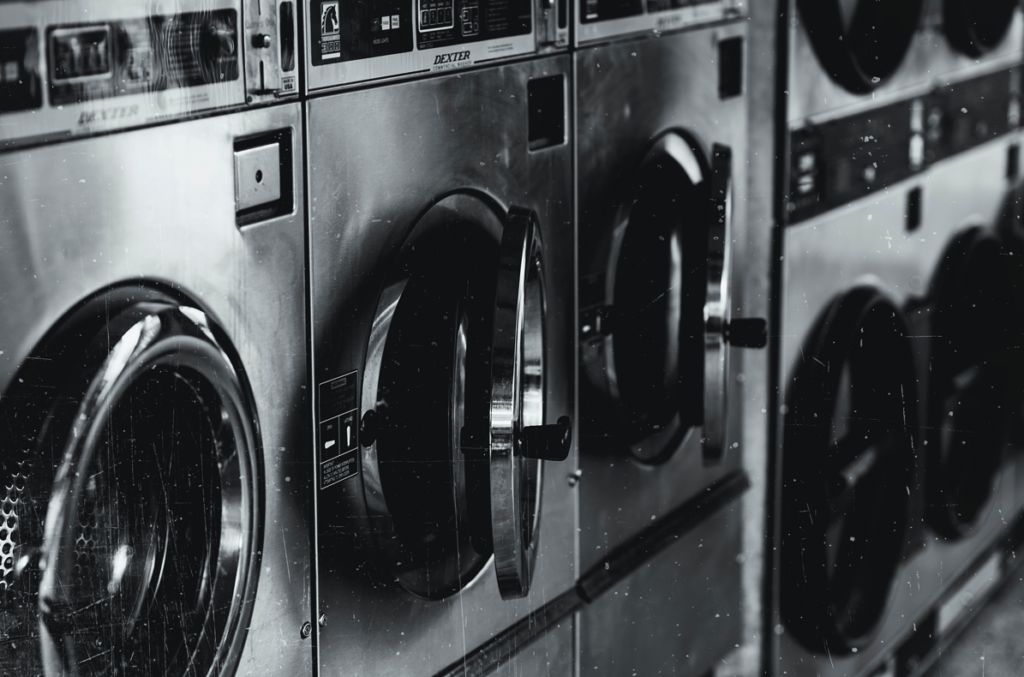
Source: pixabay
Finition mate
La finition mate est l'une des finales en acier inoxydable les plus courantes. Il fait de acier inoxydable à roulement froid. Pour obtenir un aperçu de ce type de finition, Nous pouvons constater que ce n'est pas vraiment lisse mais il est moins cher que les autres types de finitions en acier inoxydable.
En raison de sa caractéristique, il n'est utilisé que dans les industries qui sont ne se concentre pas sur l'apparence mais plus sur la praticabilité. En général, Il est utilisé dans l'architecture lorsque l'uniformité de la finition n'est pas une exigence, comme les équipements d'eaux usées, système de réfrigération, équipement de l'usine chimique, industrie de la papeterie, équipement de cuisson, Application de transformation des aliments, etc..
Finition brossée
Finition brossée, qui a été poli par une ceinture avec 120-180 grincer. Après cela, La finition brossée doit être ramollie puis elle sera en forme.
Par rapport à la finition mate, La finition brossée a un bonne esthétique. C'est lisse, lustre et moins réfléchissant. Donc, c'est une belle finition décorative pour différentes industries de fournisseur en acier inoxydable. Pour distinguer les fabricants, il peut être personnalisé, Et plusieurs changements le font bien convaincre les industries différentes.
Cependant, il y a encore des inconvénients pour cela. Le plus important est que la finition brossée réduit la résistance à la corrosion.
En raison de sa caractéristique, Ses applications sont limitées. Il est souvent utilisé dans les bijoux et les montres, conception automobile, Chauffe-eau, climatiseurs et autres ustensiles ménagers courants.
Finition miroir
Parmi les trois finitions, finition mate, finition brossée et finition miroir, la finition miroir coûte une dépense très élevée. Néanmoins, il surmonte le problème existant dans la finition mate et la finition brossée.
Le métal recouvert de finition miroir est Très lisse et réfléchissant. Cela facilite le nettoyage. D'ailleurs, Il donne une chance de masquer les conséquences du soudage et de cacher les dommages de la surface.
En même temps, La finition miroir est Conduité à la résistance à la corrosion, qui est une mise à jour de la finition brossée. En raison de sa fonctionnalité, il est largement utilisé dans les miroirs, couvertures de colonne, panneaux et réflecteurs de puits.
Facteurs à considérer
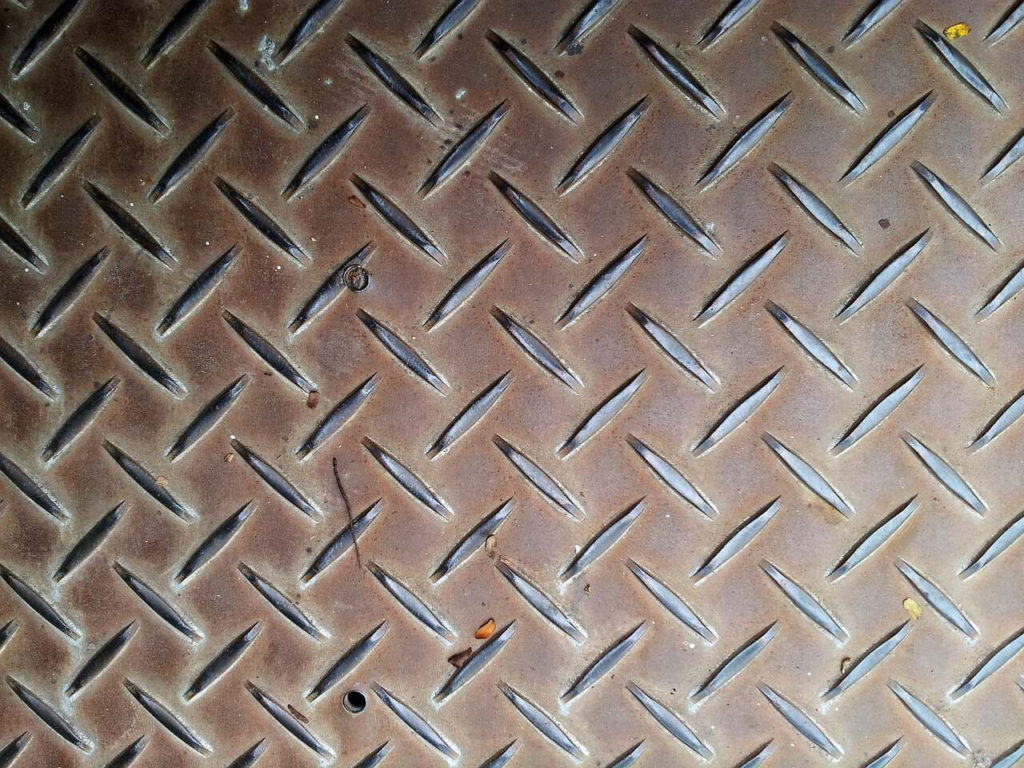
Source: pexels
Différents types de produit en acier inoxydable ont diverses exigences pour la finition, Il y a quelques considérations courantes ci-dessous:
Exigences de rugosité de surface
La rugosité de surface est une mesure de la texture d'une surface fabriquée. La rugosité peut être considérée comme de minuscules canaux entre une machine complète et la matière première. Une rugosité appropriée offre à la machine une chance de contacter l'huile appropriée. Du côté esthétique, La rugosité dépend de réflectivité, Soit brillant ou terne. Dans les paramètres de rugosité de surface, Il y a de nombreux termes qui valent la peine d'être examinés.
Préférence esthétique
Une bonne apparence est cruciale pour certains scénarios, en particulier pour l'industrie automobile. Le polissage est souvent synonyme de haute qualité.
Le polissage fait référence à l'utilisation de mécanique ou de produits chimiques pour minimiser la rugosité de surface, Afin de faire la surface brillant et plat. Le processus comprend le broyage, polissage et restauration.
Besoins de résistance à la corrosion
Pour de nombreuses industries chimiques, La anti-corrosion est importante. La théorie de la résistance à la corrosion est d'empêcher le contact entre l'eau et la surface métallique.
Certains types de finition tels que la finition miroir ont une bonne isolation électrique et une barrière d'eau, qui peut couvrir le métal pour jouer un rôle important de la résistance aux médias environnants et à la corrosion. Dans le contraire, La finition brossée peut détruire le revêtement sur le métal, et réduire sa résistance à la corrosion.
Hygiène et considération de propreté
La finition peut également être affectée par le facteur de propreté. Surtout pour la fabrication de dispositifs médicaux, Nous devons prêter attention à la considération d'hygiène et de propreté. De faibles niveaux d'hygiène peuvent fournir une circonstance adaptée aux germes et promouvoir la croissance des bactéries.
Lorsque nous tournons notre attention vers les ustensiles quotidiens, Nous devrions exiger que la finition est enlevée des substances toxiques attachées au corps humain. Donc, Les substances nocives doivent être complètement supprimées pendant le processus de production.
Normes de l'industrie pour les finitions en acier inoxydable
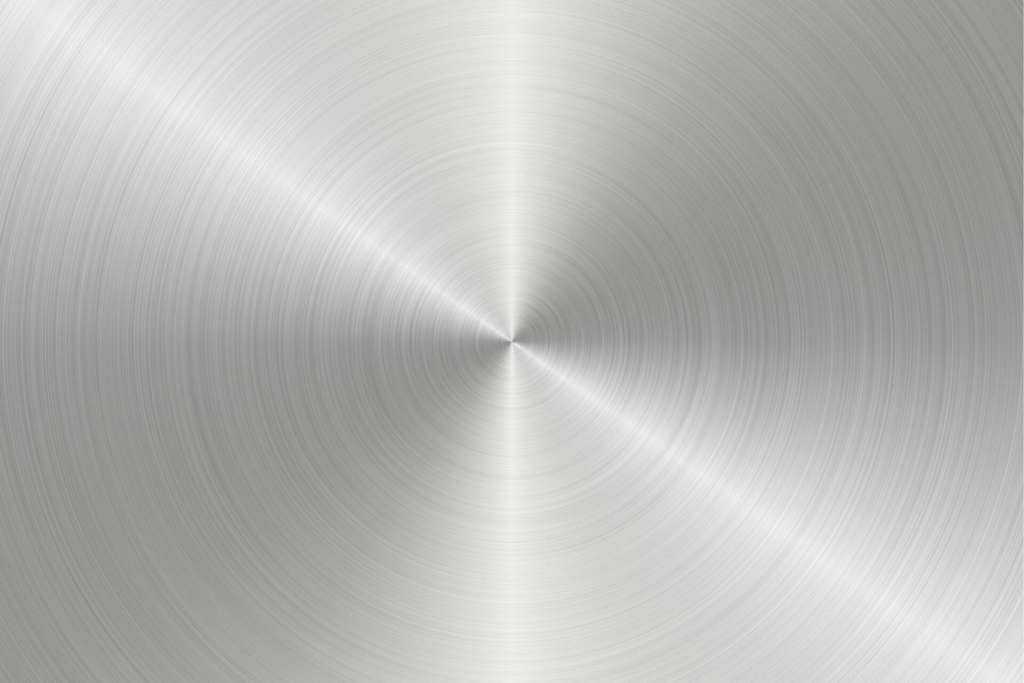
Source: pixabay
Nous pouvons avoir un aperçu des normes de l'industrie pour les finitions en acier inoxydable grâce à la désignation. Il offre une référence pour choisir Fournisseur de draps en acier inoxydable. Tous les aciers inoxydables sont des alliages à base de fer contenant au moins 10.5% chrome. Une réaction entre ce chrome et l'oxygène dans l'atmosphère produit un film d'oxyde de chrome à la surface. Cela permet au film de Immédiatement auto-réparation en présence d'oxygène en cas de dommages de surface. La couche suivante vient au moulin. Pour les finitions du moulin, il y a 1ré, 2B, 2ré, 2H et ainsi de suite.
Voici quelques détails:
- 1ré: Chaud roulé, thermique traité et mariné. Il a une surface rugueuse mais exempte de fraisage.
- 2B: À froid roulé, thermique traité, Pickled et la peau est passée. Surface lisse. C'est vraiment courant dans la plupart des scénarios, 2B est fondamental pour la plupart des finitions polies et brossées telles que les grades communs en acier inoxydable comme 201, 304, 304L et 316L.
- 2ré: À froid roulé, Surface lisse et chaleur et marinée. Il réalise une apparence de surface mate à faible réfléchie qui convient aux applications industrielles et d'ingénierie. D'ailleurs, il a un niveau d'esthétique plus élevé que 2B.
- 2H: Travailler durci. Le froid a travaillé pour une force plus élevée. Surface lumineuse.
En plus, Il existe différentes classifications pour les normes de finitions à motifs et colorés, tel que 2F, 1M, 2M, 2W et ainsi de suite, Voici les descriptions:
- 2F: À froid roulé, thermique traité, et la peau a passé des rouleaux rugueux. Parfois, Un recuit brillant ou un recuit et un décapage peuvent être effectués. C'est une surface de Matt uniforme des deux côtés de la feuille, Et il n'a pas peu d'avantages dans la réflexion.
- 1M: Conception sur accord. Un côté est plat et différentes textures peuvent être obtenues. Il est courant dans les entrées de construction en raison des textures, ce qui est utile pour éviter les accidents causés par des sols glissants.
- 2M: Conception sur accord. Un côté est une texture plate et fine est principalement utilisée pour les applications architecturales.
- 2W: Conception sur accord. Ce sont des aciers inoxydables à motifs à 2 faces dans lesquels les motifs sont roulés ou pressés. Les deux côtés avec une texture ondulée, qui augmente la force et pour l'esthétique.
Préparation et entretien de la surface
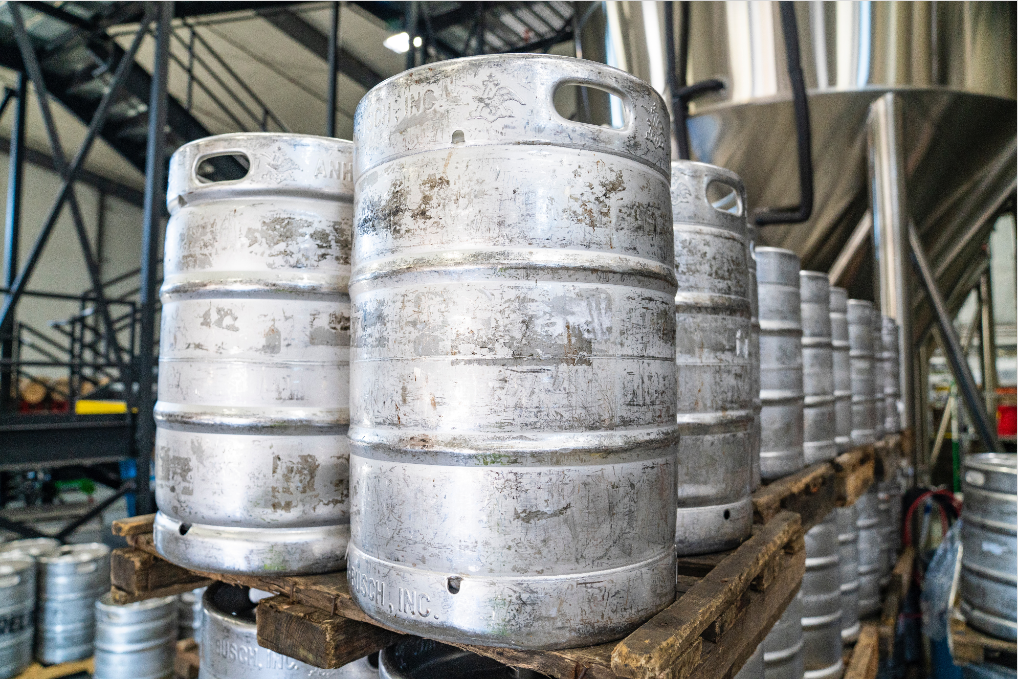
Source: pexels
L'importance des préparations et de l'entretien
La pollution de surface et les dépôts peuvent diminuer la durée de vie de la finition de surface en acier inoxydable et accélérer le processus de cassé. Beaucoup d'atmosphères, environnement industriel, L'environnement commercial et même les atmosphères domestiques provoquent des dépôts adhèrent à la surface qui pourraient être facilement corrodés.
Donc, L'entretien quotidien est nécessaire. Pour atteindre une résistance à la corrosion maximale, la surface de l'acier inoxydable doit être maintenue propre. En fait, Si les surfaces sont fournies avec une note appropriée, condition, environnement de service particulier, Procédures de fabrication et d'installation, Une bonne performance et une longue durée de vie seront atteintes. Et n'oubliez pas de faire des horaires de nettoyage corrects et réguliers.
La fréquence et le coût du nettoyage de l'acier inoxydable sont inférieurs à ceux de nombreux autres matériaux et cela dépasse souvent les coûts d'acquisition plus élevés.
Conseils
Il existe plusieurs étapes différentes, y compris la préparation avant l'installation, la maintenance lors de l'installation, Entretien de routine et autres étapes.
Il est important de remarquer que, La période de la maintenance de routine n'est pas fixe. Cela peut varier d'une fois à quatre par an pour les applications externes ou peut-être une fois par jour pour un élément dans un environnement agressif, ce qui est plus facile à corroder. Essentiellement, Cela dépend de l'atmosphère autour de l'élément.
Voici quelques outils qui ne sont pas adaptés au nettoyage:
- Outils utilisés avec d'autres métaux
- Racks de rangement en acier
- Équipement de manutention
Conclusion
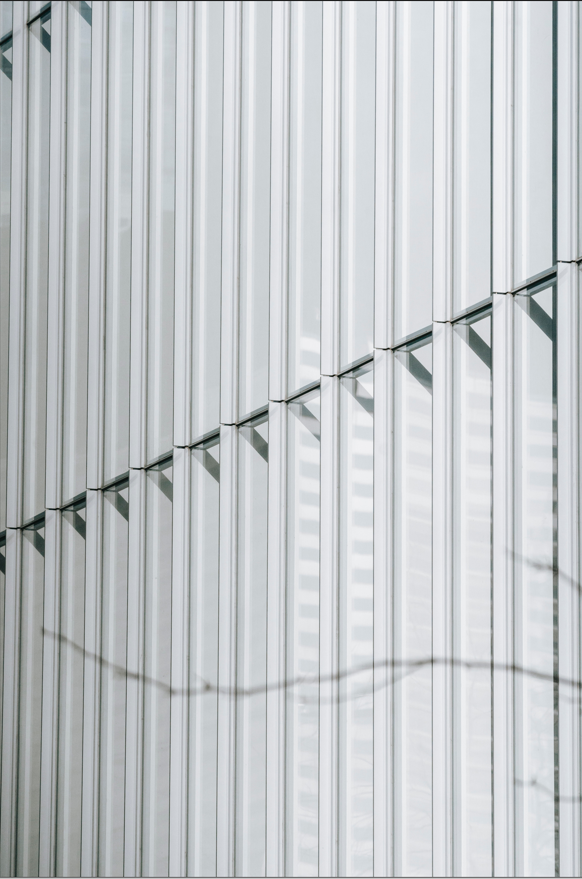
Source: pexels
Pour de nombreux métaux, La finition en acier inoxydable est essentielle. Il existe différents choix en raison des exigences variables, qui est souvent cohérent avec les caractéristiques de la finition. Finition mate, finition brossée et finition miroir sont communs dans le quotidien. Ils varient de la rugosité de surface, apparence esthétique, Résistance à la corrosion et grade de l'hygiène et de la propreté. Donc, leurs prix ne sont pas les mêmes. Pendant le processus de sélection, Nous pouvons également suivre les normes de l'industrie pour les finitions en acier inoxydable. Quoi de plus, N'oubliez pas de nettoyer et de maintenir vos finitions en acier inoxydable régulièrement.